The Rebirth
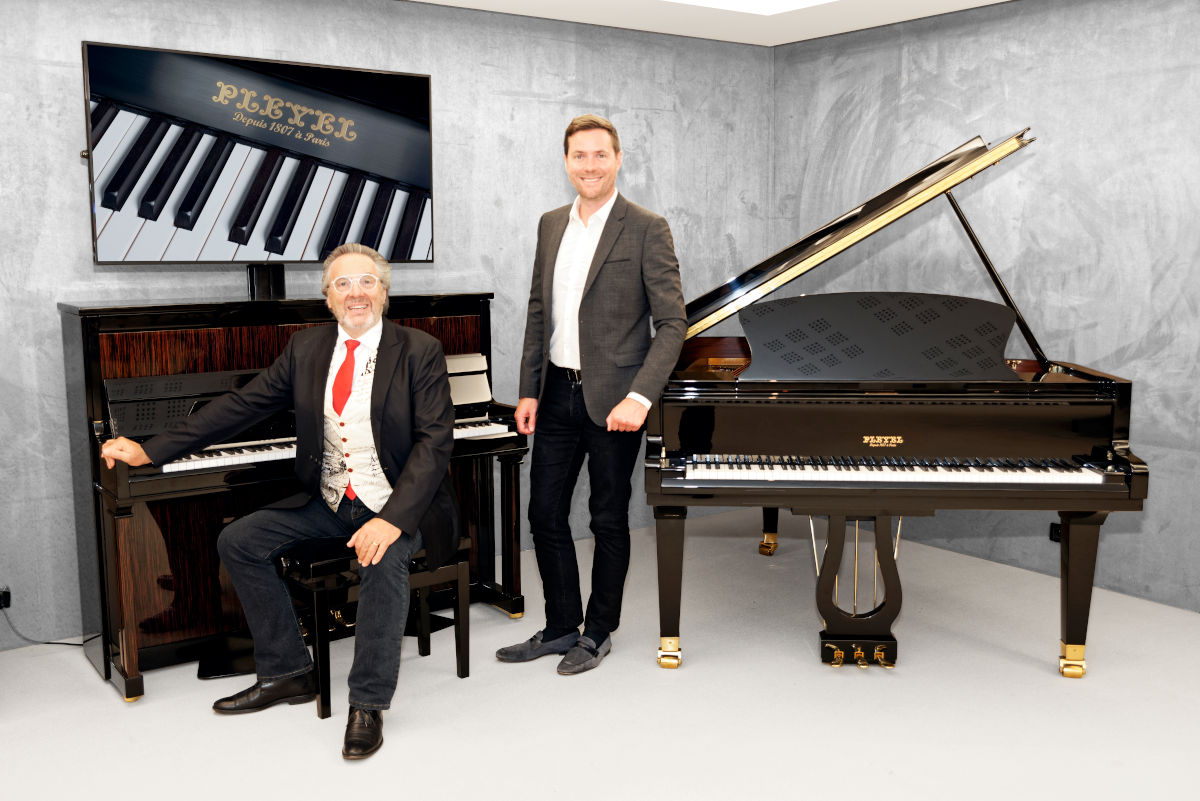
In 2017, Gérard Garnier and his son Benjamin decided to revive the phoenix from its ashes.
Despite its wreckage, the brand has remained iconic, and our intrepid entrepreneurs, at the head of the Algam group, one of the world leaders in the distribution and manufacturing of musical instruments, will take all their time to avoid falling back into the mistakes of the past. Thanks to a solid international network of industrial partners but also thanks to four long years of research and development, the first prototypes that came out of the Pleyel workshop in Nantes were applauded by the piano world. But it was not enough to find the famous crystalline but also mellow timbre which made the happiness of Chopin in the intimacy of the salons. It was also necessary to endow the Pleyel of the 21st century power and a perfect homogeneity of the registers, by marrying the sound with a more orchestral brilliance and a great reliability of touch to make the instrument sing, in order to see them regain their among the world’s great brands.
After several decades of wandering, the rebirth of Pleyel marks the return of French elegance to the piano world.
The revival of Pleyel, an exciting challenge
Like many musicians, I have always hoped that Pleyel would be reborn.
That is why, when I learned that, in absolute discretion, a team of passionate enthusiasts was preparing to make pianos sound again under the Pleyel brand, I was intrigued, curious, worried too, to the point that I couldn’t wait any longer without knowing what was being prepared concretely. A first visit allowed me to get to know both the people in charge of the project and the first grand piano under development. I don’t know who was more worried, them or me, when I put my hands on the piano. It was a very intense moment that will remain in our memories, because we were all wondering, Gérard and Benjamin Garnier who wanted to revive the brand, Patrick Horn-Wegner who developed this instrument and me who had in memory the Pleyel sound : would this instrument live up to our hopes? The minutes that followed convinced us. The Pleyel DNA was there. He was singing with a beautiful, bright, clear voice.
Yves Henry
Concert pianist - 1st Grand Prize of the Robert Schumann International Competition
Professor at the Conservatoire National Supérieur de Musique et de Danse de Paris
President of the Nohant Chopin Festival
Manufacturing
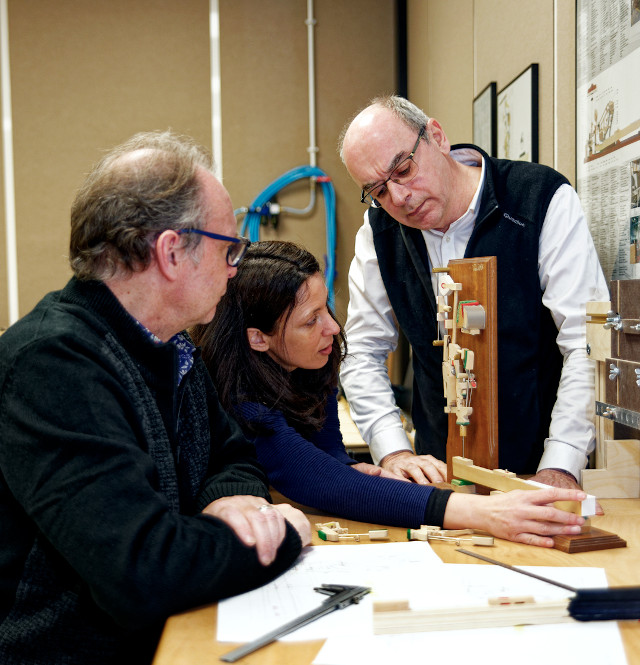
French design
The design of Pleyel pianos combines today’s technologies with the traditional know-how of piano makers. The thousands of parts of each piano are modeled in 3D using Solidworks, the powerful software developed by Dassault Systèmes. The specifications and plans produced in Nantes allow each model to benefit from cutting-edge technology in the service of the wonderful Pleyel sound.
In keeping with its tradition of excellence, Pleyel has always been a leader in the manufacture of its pianos, Pleyel is extremely demanding in the choice of components and the selection of materials: For all its soundboards, which give the piano its soul, Pleyel uses the finest spruce from the Val de Fiemme in Italy, renowned for its exceptional vibratory qualities, which has the ability to amplify musical emotion and give the instrument greater power.
The mechanism is made according to Pleyel designs and specifications, guaranteeing the highest level of performance and reliability. Pleyel uses keyboards made of top quality spruce wood that provides a very high resistance to hygrometric variations. These keyboards are particularly appreciated for their comfort and precision of execution.
The cast-iron frame, a true "backbone" of the instrument, on which the strings exert a pressure of up to 20 tons, is meticulously controlled : perfection of the casting, careful execution of its surface, maturation cycle and and strict verification of the dimensions.
All Pleyel pianos are made with strings from renowned German brands : Hellerbass for the bass strings and Röslau for the medium-high strings, to ensure the best sound, while providing stability and durability of the tuning. The Trocadero models, on the other hand, benefit from the Paulello silver-spun bass strings.
Using only the highest quality materials, Pleyel selects the different species and qualities of wood species with particular care. From storage to cutting, from humidity level to assembly, each step of the woodworking is subject to precise quality control.
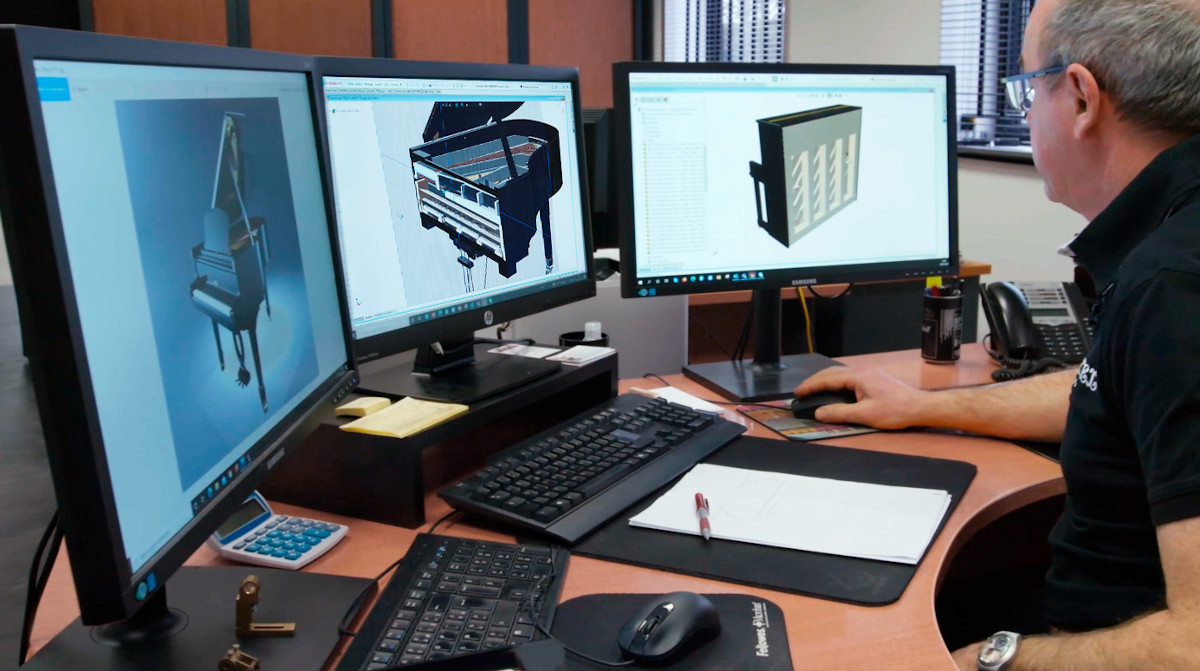
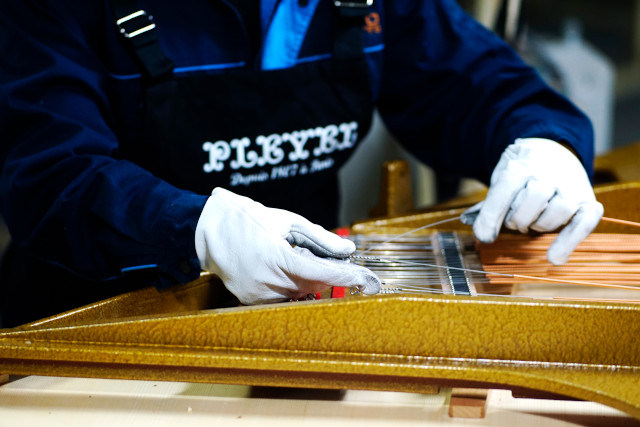
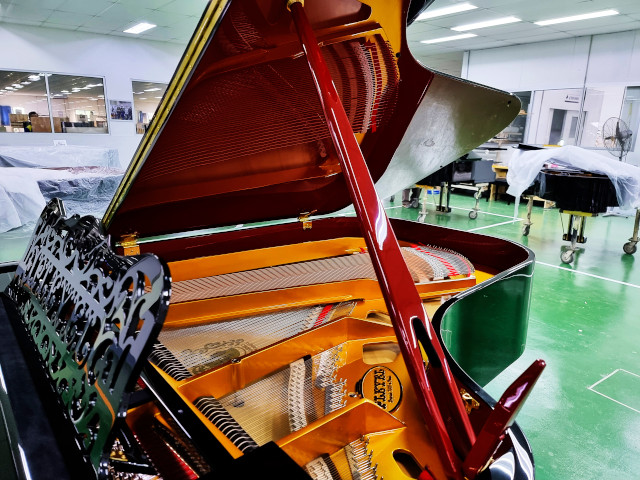
International production
How could Pleyel reconquer the global piano market?
After the sad closure in 2013 of the last Pleyel workshops in France, this fundamental question arose in order to consider the rebirth of this mythical brand.
Long months of research supported by worldwide sales statistics left Gérard and Benjamin Garnier deeply perplexed. They had to accept that the world of the 21st century was no longer the world of the 20th century, and even less so that of the 19th century, and at the same time, there was no question of accepting the slightest compromise with regard to full
respect for Pleyel quality, particularly that of its golden age.
It was therefore necessary to reconcile Pleyel quality, quantitative production and competitive price placement in order to be compatible with the new dimension of the international market.
Where should Pleyel pianos be manufactured to ensure this reconquest?
Today, about 4 500 new pianos are sold in France per year, while 350 000 are sold in China, not counting other Asian countries. What’s more, there are 30 to 40 million young Chinese who are learning the piano. These edifying figures show that today’s world is nothing like that of Camille Pleyel, who made pianos in Paris for the Western elite.
Considering these data, from an ecological as well as an economic point of view, there was only one choice: we had to produce locally.
It took several years to implement this project, which had become obvious. It was necessary to find common ground between solid industrial partners from France, Germany, Italy, South Korea, Indonesia and China in order to respect rigorous specifications.
While the Art&Design and Haute Facture collections combine Made in France with Made in Germany, the P series is assembled in Indonesia in a factory where the remarkable cabinet-making know-how carries the colors of the legendary French brand high. But above all, it benefits from a harmonic ensemble, the soul of Pleyel, produced in the Pleyel factory in Ningbo.
This P series offers an extraordinary quality/price ratio, allowing any demanding pianist to acquire an instrument with an emblematic sound.
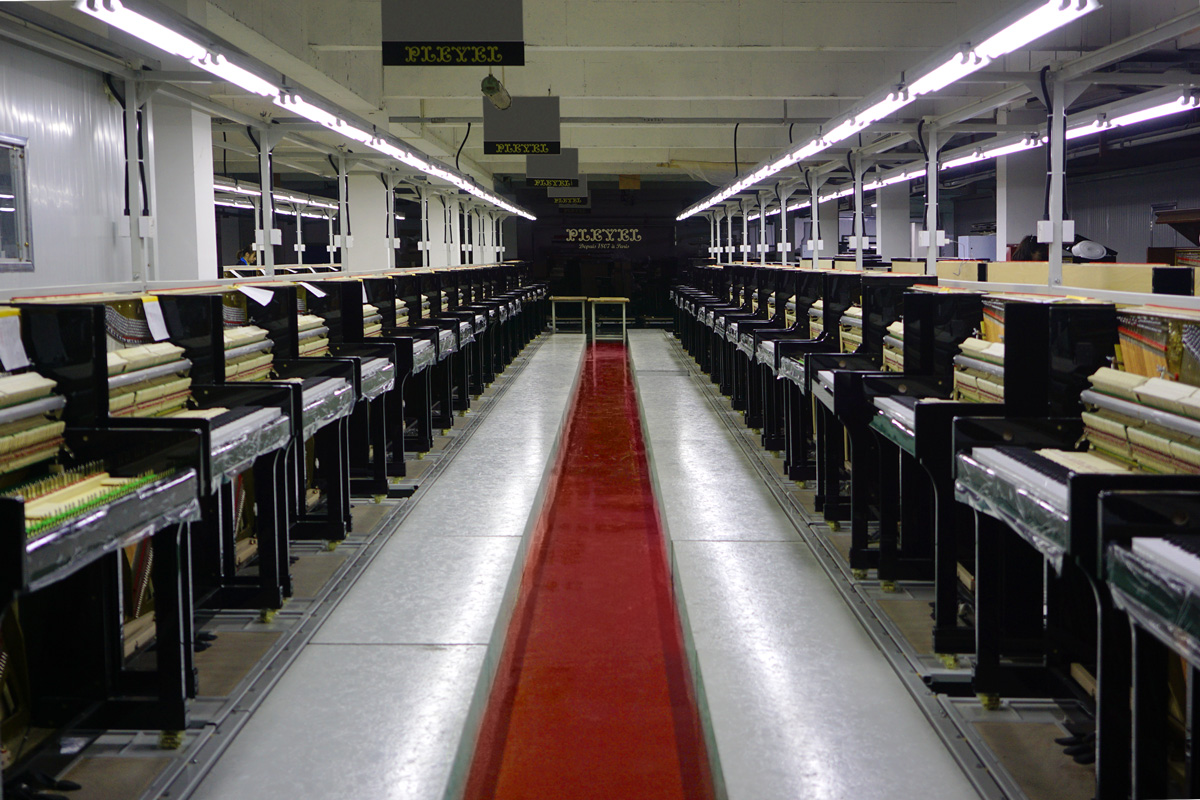
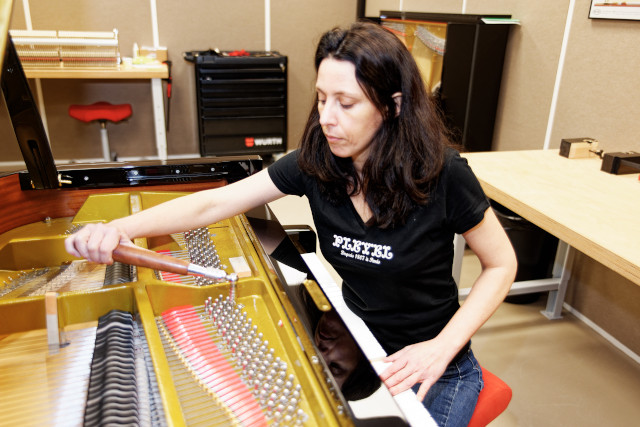
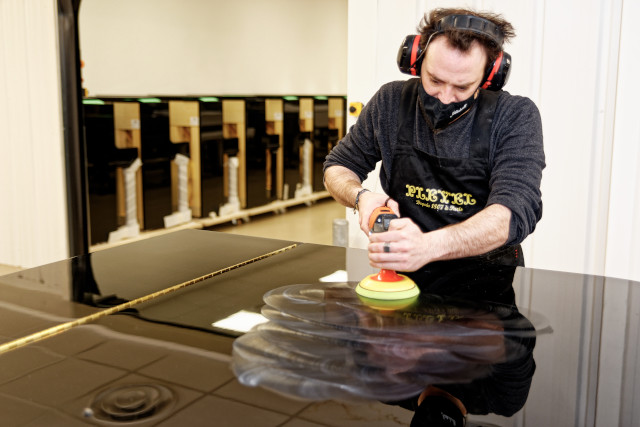
French finishing
Stabilization
As soon as the semi-finished pianos are received at the Pleyel workshop in Nantes, they are unpacked and placed in a rigorously controlled environment in terms of hygrometry and temperature in order to stabilize. After at least three months of stabilization, the tuning and harmonization procedures carried out by our expert technicians will progressively give Pleyel pianos the famous French sound emblematic of the brand.
Adjustment and tuning
At the Pleyel workshop in Nantes, our technicians will perform a precise adjustment of the height of each key, as well as the depth of depression, in order to obtain a perfect balance of the keyboard and thus a fluid and pleasant touch. They will also make sure that the hammer heads are in optimal contact with the string plane.
Four tunings are carried out for each Pleyel piano: the first at the reception inspection, the second after adjustment, the third after finishing harmonization and the fourth tuning before the piano is shipped from Nantes.
Finishing harmonization
The adjustment of the timbre, called "harmonization" or "intonation", is the ultimate point of the preparation of the piano: it is the step that will give it its sound, its tone, its harmonic richness. Harmonization consists of acting on the texture of the felt of the hammer heads, by softening or hardening them. The Pleyel technician will thus modulate the musical color of the piano by positioning, adjusting and orienting the settings, sanding and then stitching the hammer felts. This is a long and meticulous operation, taking many hours for each piano in the Pleyel workshop alone.
Polishing and final inspection
A piano must be beautiful not only musically but also aesthetically, so the last step in the preparation process is the complete reworking of the cabinet. Each instrument is thoroughly inspected, all traces, scratches and imperfections are removed and the lacquer is completely polished.
Finally, a thin layer of wax-based protection is applied to the entire case to ensure that the piano is protected against minor aggressions that could alter its shine.
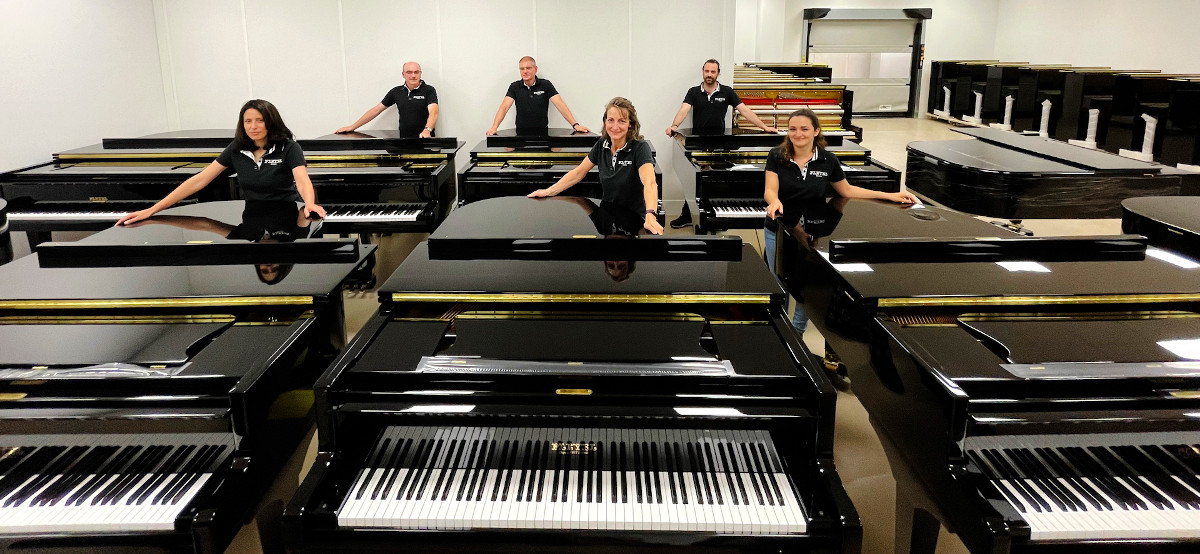